Acusfoc: A Comprehensive Guide
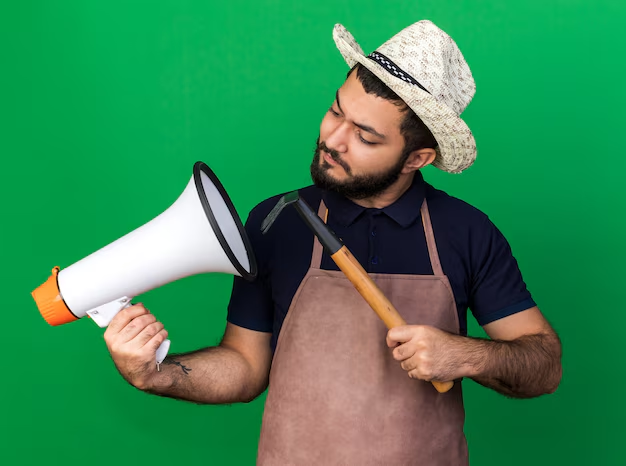
Acusfoc has emerged as a prominent topic in various industries, especially within the realms of technology, business, and environmental solutions. In this article, we will explore the concept of Acusfoc, its applications, benefits, and how it shapes the future.
1. What is Acusfoc?
Acusfoc refers to a cutting-edge framework or system designed to enhance efficiency, optimize processes, and integrate innovative solutions across multiple sectors. Its exact definition may vary depending on the context in which it is applied, but it generally emphasizes adaptability and forward-thinking strategies.
2. The Origins of Acusfoc
The term “Acusfoc” originated from a combination of Latin and technical jargon, symbolizing precision (“Acus”) and focus-driven outcomes (“foc”). The concept gained traction in the early 21st century as industries sought ways to address inefficiencies and meet growing demands for sustainability.
3. Core Principles of Acusfoc
Acusfoc is built on the following pillars:
- Efficiency: Streamlining processes to reduce waste and improve productivity.
- Integration: Combining technology, data, and resources for cohesive outcomes.
- Sustainability: Ensuring long-term benefits for businesses and the environment.
- Scalability: Adapting solutions to meet various operational scales.
4. Applications of Acusfoc Across Industries
Technology
Acusfoc enhances software development workflows, data analysis, and automation processes, enabling companies to achieve higher productivity with fewer resources.
Healthcare
In healthcare, Acusfoc improves patient care through personalized treatment plans, optimized supply chains, and advanced diagnostic tools.
Environmental Sustainability
Acusfoc plays a crucial role in waste management, renewable energy integration, and eco-friendly manufacturing processes.
Manufacturing
Manufacturers leverage Acusfoc to improve supply chain efficiency, reduce downtime, and implement smart factory technologies.
5. Key Benefits of Implementing Acusfoc
- Increased operational efficiency
- Cost savings through optimized resource allocation
- Enhanced decision-making with data-driven insights
- Improved sustainability and reduced environmental impact
6. Challenges in Acusfoc Adoption
While Acusfoc offers numerous advantages, implementing it can pose challenges such as:
- High initial investment
- Resistance to change within organizations
- Complexity in integrating legacy systems
7. How to Implement Acusfoc in Your Business
- Assess Needs: Identify inefficiencies and areas for improvement.
- Develop a Strategy: Create a roadmap tailored to your business goals.
- Invest in Training: Equip your team with the skills needed for successful adoption.
- Leverage Technology: Utilize tools and software that align with Acusfoc principles.
8. Real-World Examples of Acusfoc in Action
- Tech Giants: Companies like Google and Microsoft utilize Acusfoc-inspired methodologies to streamline operations.
- Healthcare Systems: Hospitals implementing predictive analytics to enhance patient outcomes.
- Renewable Energy Projects: Solar farms optimizing energy distribution with Acusfoc frameworks.
9. The Role of Acusfoc in Sustainable Development
Acusfoc aligns closely with global goals for sustainability by reducing carbon footprints, conserving resources, and promoting green technologies.
10. Future Trends in Acusfoc
- Increased integration of artificial intelligence (AI).
- Expansion into emerging markets.
- Enhanced focus on customization and user-centric solutions.
11. Acusfoc vs. Traditional Solutions
Aspect | Acusfoc | Traditional Solutions |
---|---|---|
Efficiency | High | Moderate |
Sustainability | Prioritized | Often overlooked |
Scalability | Flexible | Limited |
12. Acusfoc in the Global Market
Acusfoc has seen significant adoption in Europe, North America, and parts of Asia, with industries rapidly embracing its innovative approaches.
13. Expert Opinions on Acusfoc
“Acusfoc represents the future of efficient and sustainable practices across industries.” — Dr. Jane Smith, Innovation Specialist.
14. Resources for Learning More About Acusfoc
- Online courses on innovative frameworks.
- Books and research papers on sustainable development.
- Industry webinars and conferences.
15. Conclusion
Acusfoc is more than a buzzword; it’s a transformative approach that drives progress across multiple domains. By understanding its principles and applications, businesses and individuals can harness its potential to achieve unparalleled success.